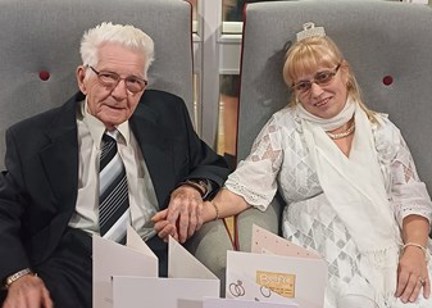
Policy Hub
Our policies are available for residents and their families to read and download. On this page you can find a list of our policies in alphabetical order.
If you require a policy in a different format including braille, large print, or a different language, please contact: communications@housing21.org.uk
This policy and procedure set out our approach to allocating Retirement Living and Extra Care properties for rent to new customers (applicants) and existing residents who wish to transfer.
Housing 21 aims to make best use of available housing by allocating homes in a fair, transparent and efficient way to older people, working in partnership with local authorities and contributing to their strategic housing function.
Shared ownership properties and those managed by Oldham and Kent PFI’s have separate allocations policies. Guernsey schemes are included in this policy however there are different eligibility criteria and processes.
Housing 21 is committed to supporting residents to live as independently as
possible for as long as practicable. This policy applies to all Housing 21
residents who may need an aid or adaptation to gain a greater level of
independence.
We understand that anti-social behaviour (ASB) can have a negative impact on our people, our schemes, our communities, and our employees. The aim of this policy is to primarily minimise ASB. However, as it is not always possible to prevent ASB also aim to be able to efficient at identifying and mitigating ASB in a way that is fair to both the victim and the perpetrator.
The Asbestos Management Plan (AMP) sets out Housing 21’s Board approved policy and procedures for managing the risks from Asbestos Containing Materials (ACMs) throughout its portfolio of properties.
Some of the buildings owned or occupied by Housing 21 were built or refurbished at a time when the use of ACMs in their construction was common. This Plan is designed to effectively manage and minimise asbestos related health risks to staff and other persons working or occupying Housing 21 premises.
The Data Protection Act 2018 (DPA18) and the UK General Data Protection Regulation (UKGDPR) provide individuals with the right to know what personal and special category information is held about them and how it is processed and protected. It also sets out requirements for organisations to adhere to when collecting and processing personal data.
This extends to personal data captured on CCTV. CCTV and other surveillance systems have a legitimate role to play in helping to maintain a safe and secure environment for all our employees, residents, carers, and visitors.
The Data Protection Act 2018 (DPA18) and the UK General Data Protection
Regulation (UKGDPR) provide individuals with the right to know what personal and sensitive (special category) information is held about them and how it is processed and protected. It also sets out requirements for organisations to adhere to when collecting and processing personal data.
This extends to personal data captured on CCTV. CCTV and other surveillance
systems have a legitimate role to play in helping to maintain a safe and secure
environment for all our employees, residents, carers, and visitors.
The Social Housing Regulation Bill makes it clear that landlords must place residents at the heart of their services.
Housing 21 is committed to ensuring residents have as much choice as possible about services at their schemes.
There may be occasions when we as the landlord have to make some decisions in keeping with health and safety or as part of a wider duty of care.
For everything else, we want residents to be able to have their say and influence decisions.
Where it is not possible for choices to be made by just one individual, we will
involve everyone to make a consensus decision.
All decisions, whether made by us in keeping with health and safety or through a consensus agreement, will be clearly communicated and explained.
Housing 21 is committed to delivering quality services to agreed standards. We recognise that we may occasionally fail to achieve our agreed standards or service, and this may result in causing distress, loss or inconvenience to our residents or other stakeholders. We will consider awarding compensation where it is shown that an individual has suffered due to the lack or failure of service within the control of Housing 21.
We are committed to delivering high-quality services and value all feedback, both positive and negative. Compliments help us recognise good practice, while complaints allow us to improve. This policy outlines our clear, two-stage process for handling complaints fairly and efficiently, in line with the Housing Ombudsman’s Complaint Handling Code. Our approach ensures concerns are addressed promptly, promoting learning and service improvements across Housing 21.
This policy ensures the secure storage, use, and replacement of keys across our extra care and retirement living schemes. Each scheme has an electronic key safe, accessible remotely in emergencies while maintaining resident security. It provides controlled access when needed, such as in a Scheme Manager’s absence. The policy also includes guidance for employees on accessing a resident’s home in emergencies or when assistance is required.
Read the full Control of Scheme Keys and Use of the Key Safe Policy
This policy sets out Housing 21’s approach to dealing with damp and mould in homes and communal areas
that we maintain. It covers the services we provide to tenants who rent their home under a tenancy
agreement.
For leaseholders, we will meet the responsibilities as set out in the terms of the lease.
Housing 21 is committed to supporting residents experiencing or at risk of domestic abuse. We take all reports seriously and work sensitively to provide assistance, ensuring residents feel safe and heard. This policy outlines how we respond, offering guidance, working with partner agencies, and enhancing safety and support. We also provide clear guidance for employees and aim to reduce the stigma surrounding domestic abuse.
Housing 21 is committed to ensuring the electrical safety of our residents’ homes and office premises. This policy sets out how we meet our legal responsibilities by maintaining safe electrical installations, conducting regular risk assessments, and implementing appropriate safety measures. We take proactive steps to prevent and control electrical risks, ensuring our properties remain safe throughout each tenancy.
Housing 21 is committed to maintaining fire safety across all our properties to protect residents, employees, contractors, and the public. This policy sets out our approach to managing fire risks, ensuring compliance with legal responsibilities, and providing a safe living and working environment. Developed in consultation with Cambridgeshire Fire and Rescue Service, it outlines the steps we take to prevent fire hazards and respond effectively.
Housing 21 is committed to ensuring the safety of residents, employees, contractors, and visitors in properties with gas-fuelled appliances. This policy sets out our approach to servicing and maintaining gas appliances, chimneys, and flues to minimise risks. We conduct annual gas safety inspections, including in properties with inactive gas meters or service pipes, to ensure compliance and protection for all.
Housing 21 is committed to providing safe and inclusive gym facilities for residents to promote health and well-being. This policy outlines the conditions for gym usage, health and safety requirements, and induction processes to ensure residents and other approved users can safely enjoy these facilities.
Housing 21 is dedicated to supporting residents in maintaining financial independence for as long as possible. Employees will only assist with money management as a last resort, ensuring safeguards are in place when support is needed. This policy outlines when and how financial assistance may be provided, the necessary documentation, and the importance of protecting both residents and employees through clear procedures.
Housing 21 is a pet-friendly organisation that recognises the positive impact pets can have on residents’ wellbeing. Residents may keep pets with permission, following our guidelines to ensure responsible ownership. Where pets may affect communal areas, agreements will be made in line with our Choice and Consensus Policy. This policy outlines the conditions of pet ownership and how Housing 21 supports residents in caring for their pets responsibly.
Housing 21 is committed to maintaining the safety and reliability of lifts and lifting equipment across our properties. This policy ensures that all passenger lifts, hoists, stairlifts, and through-floor lifts are regularly inspected and maintained to a high standard. By following legislative requirements, we aim to minimise risks to residents, employees, visitors, and contractors, ensuring safe and accessible environments for all.
Read the full Lifts and Lifting Equipment Policy and Procedure
Housing 21 recognises the importance of mobility vehicles in supporting residents' independence and social inclusion. This policy provides guidance on their safe use and storage, ensuring the wellbeing of residents, employees, visitors, and contractors. It outlines the process for obtaining permission to keep a mobility vehicle and promotes responsible ownership to help minimise health and safety risks across our schemes.
Housing 21 supports residents who wish to swap homes through a mutual exchange. This process allows social housing residents to exchange properties with others, subject to landlord approval. Most residents have the legal right to do so, and this policy ensures applications are handled consistently and in line with legislation. It sets out our approach to processing requests fairly and efficiently.
Housing 21 is committed to ensuring that all residents’ homes and office premises remain safe and secure. This policy outlines our approach to property compliance, detailing our legal responsibilities under health and safety legislation. It sets out how we manage risks, maintain buildings, and ensure full compliance with regulatory requirements. The policy is regularly reviewed and updated in response to legislative changes to keep our properties safe for all.
Housing 21 is committed to ensuring all residents can access our services and information. This policy sets out our approach to making reasonable adjustments and providing alternative formats for documents and communications when needed. It also supports employees in managing these provisions while ensuring compliance with the Equality Act 2010 and the Regulator of Social Housing Consumer Standards.
Read the full Reasonable Adjustments and Provision of Alternative Formats Policy
Housing 21 is committed to maintaining high-quality homes through a responsive and cost-effective repairs service. This policy outlines our responsibilities, ensuring residents know what to expect from us. It aligns with tenancy and leasehold agreements and meets regulatory standards. Supporting documents, including the Residents’ Handbook and Repairs Handbook, provide further guidance on repairs processes and expectations.
Housing 21 is committed to providing high quality homes in a safe and inclusive environment for residents. This policy outlines our approach to tenancy management, support to sustain tenancies and how we tackle tenancy fraud. It includes:
- the types of tenancies we grant
- how we support residents to sustain their tenancies and prevent unnecessary evictions.
This Policy applies to residents living in rented accommodation, it does not apply to those with Leasehold or Commercial agreements.
Housing 21 is committed to ensuring the safety of residents, employees, and visitors by maintaining high water hygiene standards. This policy outlines our approach to managing water systems, preventing risks such as Legionella, and meeting all relevant legal and regulatory responsibilities. We take all reasonable precautions to ensure the water systems in our properties remain safe and well-maintained.
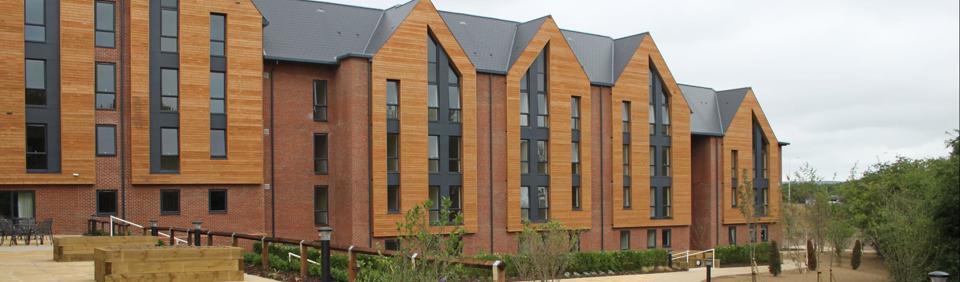
Resident guides
Need something different?
Explore a range of useful guides and resources designed to support you in your home including your latest Resident Handbook.